TIMBER WALL CONSTRUCTION - LIKE LEGO EFFICIENT WALL MODULES - DURABLE AND ERECTED IN NO TIME AT ALL
Older 3-D Image of refugee accommodation
Due to the unsolvable environmental problems in cement production and the extraction of building sand, completely new paths could and should have been taken in the construction sector a long time ago. My approach - sustainable building components in modular construction, as a scalable plug-in system.How can these modules be produced by both prefabricated house manufacturers and laymen?In this concept, stackable sandwich wall modules form a mobile and deployable variant. The example corresponds to my idea of a garden home, here with 35 m² of superstructure area and a height of 5 metres.
The modules can be produced in just a few days and can be joined together using a tongue and groove system, allowing them to be raised together with the upper storey.
Ready for shell construction - with windows, doors and internal staircase - my calculation of the material costs (with May 2023) comes to ~15,000 euros.
Each of the components/elements weighs approx. 20 kg. The modules can be manufactured on site* or delivered prefabricated. As tongue and groove elements, the 80 modules here can be handled by 2 people without the need for a construction crane or scaffolding. Around the base plate and its staggered substructure, the components are installed horizontally, efficiently and quickly.
The coarse chipboard panels OSB3 can usually remain in their standard size of 2050 x 625 cm. Styrofoam insulation** is placed (using a template) diagonally offset by 15 cm between two 12 mm thick coarse chipboard panels. This results in two module edges on the tongue and groove side. For this purpose, the OSBs receive an adhesive mortar spread with a notched trowel around their edges and in the centre. The (e.g. 12 mm) polystyrene boards (EPS) embedded in between form a durable module body. After the adhesive has dried, the numbered N/F components are pulled up to form walls using a plug-in system - similar to LEGO - whereby the modules are lined up at the corners of the house in staggered rows.
The corner joints are secured from the inside using 4x4 cm perforated angle profiles (Shelf stand) and 18 cm long nails, hole by hole. For the 18 mm nails (5 mm Ø), the two rows of holes on the coarse chipboard panels are pre-drilled with 4 mm holes.
The nails, which are only 95% countersunk, enable easy removal so that the numbered components can be reassembled at another construction site.
Cables and other installations can be laid discreetly behind ceiling, corner and plinth grooves.
A simple wooden stringer staircase leads to the sleeping area on the upper floor - with clothes storage and a 7 m² conservatory. Landscape photographic wallpaper could give the rooms a pleasantly calm visual effect of depth.
These load-bearing modular buildings are fire-resistant***, earthquake-resistant and fastened at the outer corners with 75 cm long storm anchors. The walls never get damp and have no thermal bridges.
Three horizontal window elements (2x0.6 m) and the patio door (1.6x1.8 m) provide both interior rooms with plenty of daylight. The triple-glazed window elements integrated into the wall modules remain closed in favour of heating cost-saving ventilation****.
Finally, the finished building carcass is given a reed mat cover, which is attached to counter battens. The mats are spray-impregnated on both sides with water glass (against weathering and flammability). They can also be given any exterior colour design. Cuttings of evergreen ivy can then grow up around the base - creating a shaded and ventilated green façade in a short space of time. The green façade plus OSB and polystyrene provide good insulation against short-wave heat radiation in summer.
The seven metres are assigned to the east and west fronts, while the five metres of the broad façade face north/south.
A 10 m² vacuum tube collector leans against the south wall. A 500 litre buffer tank above it heats a copper pipe laid as a skirting board. The cylinder also supplies the washing machine and dishwasher with hot water.
ThinFilm foils or PV panels for the house electricity can be installed over the entire surface of the 50 m² pitched roof with overhang and, in conjunction with PV batteries, can also cover the additional operation with a heat pump split air-conditioning heating system - such as that from the test winner Dimstal-eco-smart Inverter - QuickConnect.
The rainwater from the roof ends up in 2x200 litre barrels and is used to irrigate the kitchen garden.
Whether as a school, shop, warehouse, ambulance, workshop or new living space - this universal construction method can be scaled spatially as required and built statically multi-storey with correspondingly strong OSBs.
From tiny houses to large-scale projects - thanks to the low weight load and inherent structural load-bearing capacity of this type of wall, even higher storeys can be added to conventional buildings quickly and at low cost.
A durability/inhabitability of up to one hundred years can be expected. Afterwards, all components of such modular buildings are available for reuse.
* Tool requirements: e-Styrofoam cutting table; e-screwdriver, jigsaw, etc. - cause only low noise and dust generation.
** Rock wool, natural fibre clamping felt or cellulose flakes could also be sufficient against negative thermal convection, but only polystyrene - laid without joints - is also free of moisture at the dew point. Also, only EPS offers the statically favourable load-bearing capacity of a slim, load-bearing modular wall. EPS can also be easily separate well from the OSBs using hot wire and
recycled afterwards - by FZ-Recycling GmbH & Co. KG, for example. The adhesive cement can also be rubbed off the OSBs.
*** KRONOPLY OSB/3 EN300, for example, offers boards that fulfil the criteria for use in fire protection construc fire protection constructions according to DIN 4102-4 in fire resistance class F30.
**** Automatic room ventilation with heat recovery: A 5 m long, 80 mm Ø aluminium flex hose concealed in a ceiling cove is connected - behind its 110 mm wall outlet - to an interval-switched fan. A piece of hard zig-zag cardboard drawn into the hose ensures good turbulence of the stale warm air and thus good temperature transfer to the fresh air flowing into the throat channel. The air is directed vertically 2 metres downwards from the branch of the 80 mm inlet as a corner fillet. The negative room pressure generated by the 80 mm exhaust air ventilator causes the fresh air to flow in automatically at the open end of the corner cove. The cove, which is made of coated hard cardboard, with its room air heat in contact with the cardboard, also transfers temperature to the incoming fresh air.
* PV-Folien produce e.g. :
ARMOR solar power films, Heliatek ®, Flisom, Alwitra-Evalon cSi ®, FirstSolar®, Nanosolar ®.
Everyone is free to implement this as yet untested approach. Building and prefabricated construction companies could endeavour to obtain correspondingly evaluated approvals.
This LINK: https://gemini-next-generation.haus shows an interesting energy and home climate technology approach by CEO
Roland Mösl.
_________________
Source IPCC: Cement production emits more CO² than air traffic and shipping combined!
It is therefore imperative to reduce CO2-polluting cement production and the ecological consequences of sand mining. After all, the food chain of marine life begins with micro-diversity, which is primarily based on sandy sea beds!
May countless of these structures be built from renewable trees. Even if not every tree is nature and forest is not the same as forest.
SEE: YOUTUBE: PETER WOHLLEBEN - THE SECRET LIFE OF TREES.
© by Thalhammer Michael - Vienna on 02.09..2022
===============
This construction method is also well suited for migration needs and reconstruction after war damage! The consequences of war, flight and displacement are increasing worldwide. Many cities are uninhabitable or uninhabitable and legions of people have no or only miserable living space. However, the usual containers and tents - for people - are not suitable accommodation in the heat or cold; they are also bulky to transport.
Whether as a school, ambulance, office, shop or housing requirement - the construction method described above can be used to save space, especially with storeys. These elements can be set up by 2 - 3 people using N/F plug-in connections to suit the respective room utilisation.
To counteract short-wave solar heating, it is particularly advisable - especially in hot regions - to cover the building with reed mats and shade it with ivy.
Stackable wall modules are a mobile and frequently deployable solution for almost any purpose.
The drawing shows an example of many possibilities.
Here as a multi-purpose building with variable room partitioning. This approach requires only simple hand tools for its construction (as well as for its dismantling for reuse).
These living spaces are based on a foundation-free 120 m² mansard roof, with a central 60 m² communal space arranged around the main room. The total interior space in this example covers 120 m². 63 m² are added as floor areas - divided between the 18 units.
This approach would be suitable for support communities whose aim is to offer refuge and encounters for people in crisis from different walks of life.
The most essential, applicable house rules would be: # ... to respect each other. # ... be there for each other as a "small family" and stick together. # ... to help organise the daily structure and group activities as much as possible.
In this example, the central 60 m² of the NurDach serves as a work and recreation room. Small products can be made there in co-operation or various services can be offered.
Smoking and drinking are only permitted outside the building!
Two of the rooms are reserved as an office (or night-time standby room) and as storage - this would result in 18 units of equal size.
Each of the 16 private rooms has 4 m² of living space measuring 3 m x 1.23 m and a room height of 2.5 m and a small window to the day room. Above this is a 3.5 m² attic room, which is accessible via a folding attic staircase.
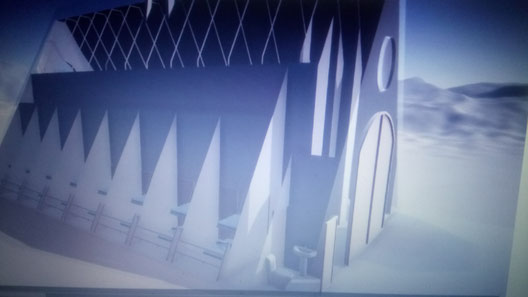
All sliding doors to the living area can be locked by their respective occupants. In addition to the bed equipment, it also has a wardrobe, folding table, folding chair, a mini-eco-heater, LED lamps and DAB radio with headphones - as well as an attachable extra bed for children who may also move in; and adjustable ventilation.
Residents can keep their sleeping hours around the clock, but there is a general night's rest from 11 pm to 7 am.
The two WCs located in the canopy, the washbasin and the shower have their 12V LED lighting switched by motion sensors.
The shower water is regulated to be drawn every three minutes so that there is enough hot water for everyone. There is also a washing machine and three fridges for residents to use.
In cold weather, the 10 x 6 metre central room of the "NurDach" also provides a place for children and their parents to play and snuggle up. Screens form a partition from the rest of the space, which all residents can use for their various activities.
The kitchen, dining area and sanitary facilities would be located outside under one roof.
The panels hanging down at the outer edge are rolled up in strong winds. These mats are protected against fire and weathering with a coat of water glass.
There is also a children's play tower with 2 swings, sandpit and slide fenced in by Immergrün under this canopy.
The house and porch would also be surrounded by a hedge, raised beds and berry bushes.
Two 1000 litre hot water tanks are located centrally in the porch - they are connected to the hot water collectors on the south-facing roof. This space is also used by a PV module to supply the 12V consumers with electricity.
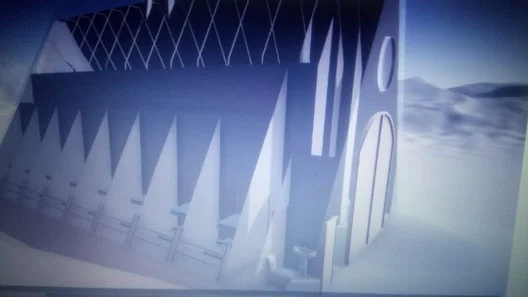
Leisure activities include badminton, table tennis and a bookshelf as well as sewing, pottery, language courses, music, painting, dance, gymnastics and more. The carers offer a varied, colourful daily structure - according to their own talents and focus. Whether it's an excursion, singing, meditation or a basic PC course - there are always encounters and useful things on the programme.
By coming together on a daily basis to work and spend leisure time together, there are also interdenominational and non-political human conversations.
The project costs a total of around €50,000 per unit.
Most of the goods would come from DIY stores, which would then also appear as the main donors.
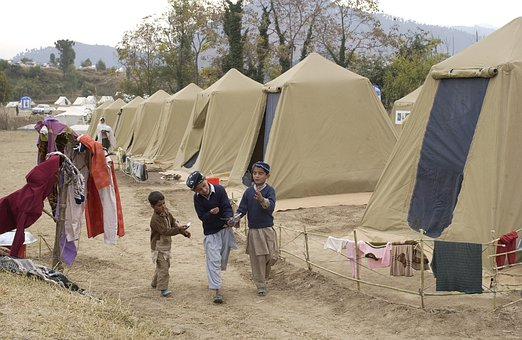
More you see in the older 3-D-Video and to www.vimeo.com/293395008
ON THE WAY TO THE LIGHT LEAVE NO ONE BEHIND ! Peter Rosegger
- -------------===========------------- -
Solar thermal energy, for example, is a very important building block here, along with other aspects: "Why generate electricity first and then heat from it? That's what solar thermal energy is for." Dr Gerhard Rimpler heard this question and the response to it quite frequently almost ten years ago. However, with the unusual idea of using photovoltaic systems to produce hot water, his company my-PV initiated nothing less than a paradigm shift in solar heat generation. Since then, the guiding principle of "cables instead of pipes" has really shaken up the solar market. The "revolution in solar thermal energy" began in 2014 with the ELWA product! https://www.my-pv.com/de/news/photovoltaikwaerme-vs-solarthermie-kosten-und-flaechenvergleich/ According to solar house pioneer Josef Jenni, " ... hot water panels are the gentlest, most environmentally friendly and most efficient technology. "Heat is generated as heat, stored as heat and consumed as heat". Solar thermal energy is collected close to where the heat is needed, for example on the roof of buildings. This heat can also be stored on site relatively easily. In addition, the use of solar thermal energy saves a lot of electricity. The energy transition would therefore primarily be a "heat transition", see www.sonnenhaus-institut.de.
In order to support the 1.5° climate target, the spatial planning authority must take more effective action against further urban sprawl! In addition, sustainable, self-sufficient energy supply must immediately become a new, mandatory building standard.
In general, buildings in rural areas should not be less than 150 m² and should not be less than three storeys high. It would also be right to demand that the "global players" in the retail sector, who have been reclassified as building land and account for a relatively large proportion of soil sealing, and who only build at ground level but on a large scale under a handful of brand or company names on countless village outskirts, be subject to restrictions. They should subsequently add 1 - 3 storeys and a vertical roof garden with generally useful living space. In addition, the car park areas previously sealed with asphalt were to be replaced with functional paving to allow rainwater to be absorbed.
With the costs of building sand and energy sure to continue to rise, there will inevitably be a change in our construction practices. A switch from cement, sand and reinforcing steel to, for example, OSB with EPS insulation - as well as applied PV film façades - would be sustainable, future-proof and therefore desirable.
The installation of vertical wind turbines (Bladeless-Vortex), which have not yet been able to gain acceptance - probably due to the current wind turbine lobby - would also generate energy. The same applies to PV solar films, which should be given preference over heavy silicon panels in aluminium frames.
_________________
These approaches could and should also be adopted by the construction industry as well as by the UNHCR, FAO or UNIDO for further implementation.
~~~~~~~~
~~~~~
~~